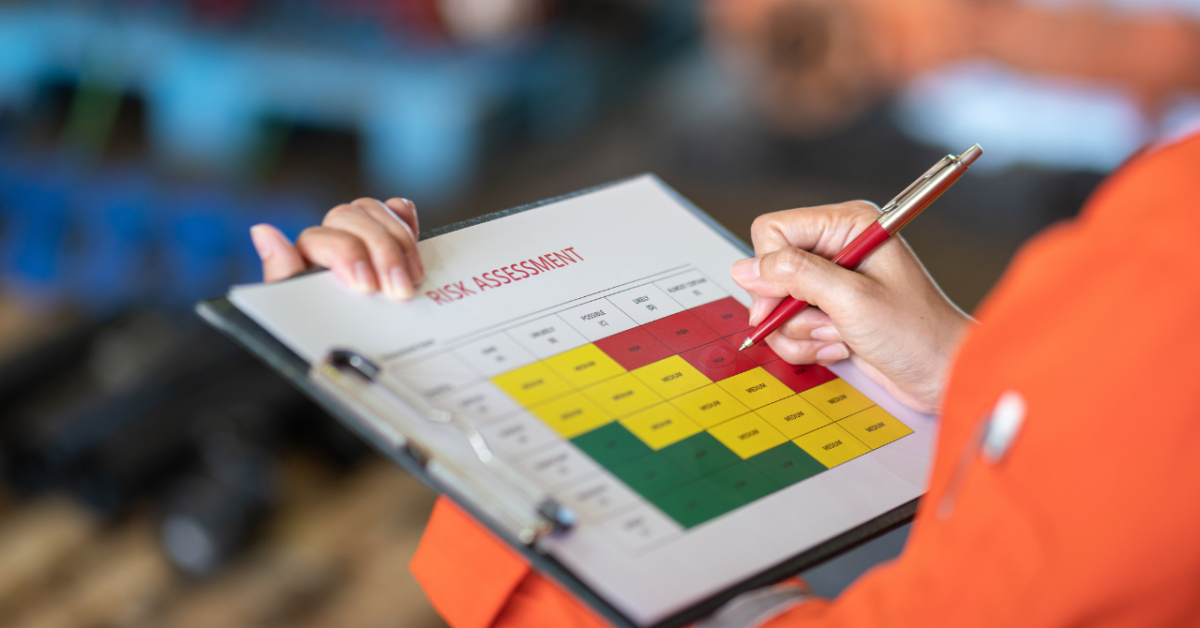
FMEAとリスク優先度(RPN)
リスク優先度(RPN)の定義と概要
リスク優先度数(Risk Priority Number: RPN)は、製品やプロセスにおけるリスクを定量的に評価するための重要な指標である。
これは以下の3つの要素の積によって算出される。
重大性(Severity: S)×発生確率(Probability: P)×検出可能性(Detection: D)
この計算方法は、経済性を考慮した実用的なアプローチとして広く認識されている。各要素は通常1から10の範囲で評価され、結果として得られるRPNは1から1000の範囲となる。
リスク優先度の評価プロセス
リスク優先度を適切に評価するためには、体系的なアプローチが必要である。評価プロセスは主に次の二段階で実施される。
- 第一段階では、重大性とリスクの発生確率を詳細に分析し、それらを組み合わせたリスクマトリックスを作成する。この段階で、各リスクの基本的な分類が決定される。
- 第二段階では、第一段階で得られたリスク分類と検出可能性を組み合わせて評価を行う。これにより、最終的なリスクの優先順位が決定される。この優先順位に基づいて、対策の実施順序が決められる。
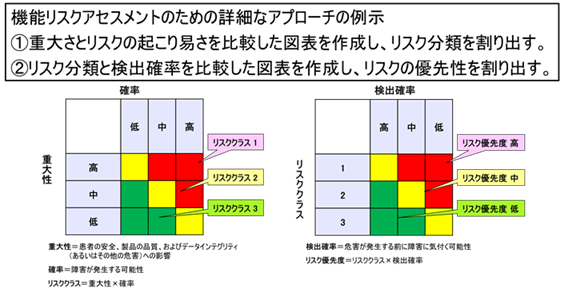
リスク優先度(RPN)の求め方
FMEAの歴史的発展
FMEA(Failure Mode and Effects Analysis:故障モード影響解析)は、製品やプロセスの潜在的な故障モードを分析し、その影響を評価するための体系的な手法である。
1940年代、アメリカ軍において信頼性向上を目的として最初に導入された。その後、1960年代に宇宙開発分野へと応用が広がり、特にNASAのアポロ計画において重要な役割を果たした。この時期のFMEAの成功により、その有効性が広く認識されることとなった。
1970年代に入ると、フォード社が自動車産業への導入を先導し、製造業における品質管理の標準的なツールとして確立された。日本においても同時期から、量産開始前の製品評価プロセスにFMEAが組み込まれるようになった。
特筆すべき発展として、トヨタ自動車が開発したDRBFM(Design Review Based on Failure Mode:故障モードに基づくデザインレビュー)がある。これは従来のFMEAを発展させ、特に設計変更や製造プロセスの変化点に着目した手法として確立された。
故障モードの詳細な理解
故障モード(Failure Mode)とは、製品やシステムにおいて発生する可能性のある故障の形態を体系的に分類したものである。具体的には、機械的な摩耗、電気的な断線、材料の劣化などが含まれる。
FMEAを実践する際には、各プロセスにおける様々な要素の変化点を詳細に分析する。これには以下の要素が含まれる。
- 設備の状態変化
- 作業者の交代
- 作業方法の変更
- 使用部品の変更
- 環境条件の変化
などである。
例えば、製造ラインにおいて作業者が交代する際には、技術レベルの差異による品質のばらつきが潜在的な故障モードとして考慮される。
このように、故障モードの分析では、物理的な故障だけでなく、人的要因やプロセスの変化に起因する潜在的な問題も包括的に考慮される。
これにより、製品やプロセスの信頼性向上に向けた効果的な対策を講じることが可能となる。
関連商品