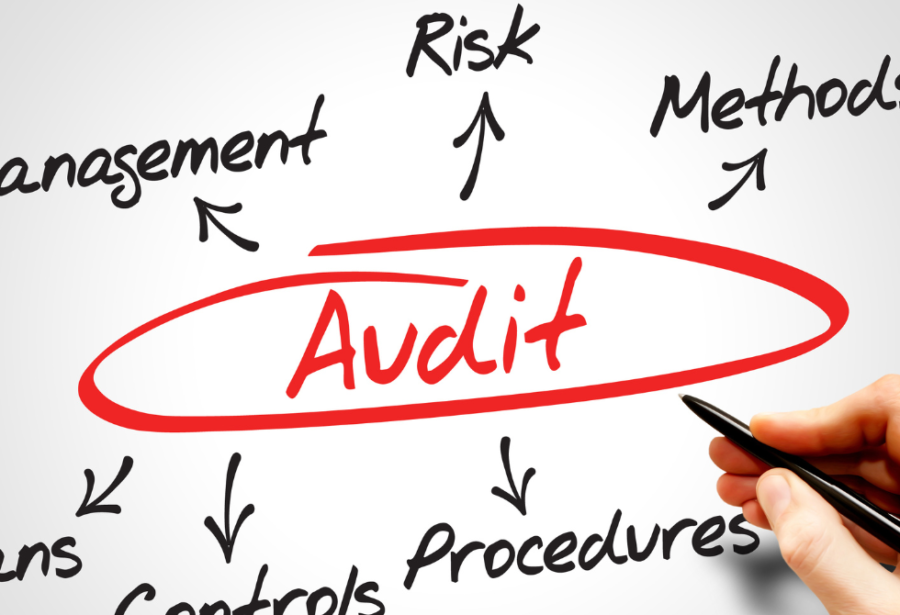
供給者からの受入検査
供給者からの受入検査
前回は不適合品管理について考察した。
医療機器に限らず、製造における3原則は、不良を入れない、流さない、出さないである。
今回は、供給者からの部品等の受入検査(受領検査)を考察してみたい。 図にあるように、受入検査は受領検査・中間検査・最終検査に区別される。
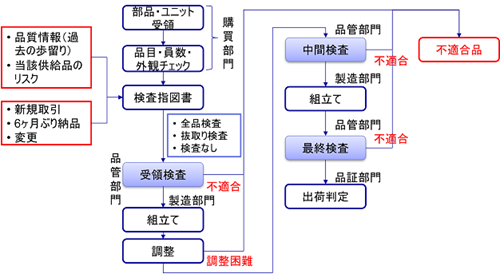
筆者の経験では、受領検査(供給者からの受入検査)を省略して工程内で不具合等が発見された場合に、当該部品を取り外している企業が多い。
これでは、もともと購買した部品に欠陥があったのか、組み立て工程中に壊してしまったのかが不明となってしまう。
また、リワークのための時間や手間もかかってしまう。
受領検査を全く実施しないということには問題があるが、一方で受領検査自体にも時間やコストがかかってしまう。特に大量に購買する部品等においては、全品を検査することは困難である。
そこで、適切なレベルで受領検査を実施することが望まれる。
全品検査
まず全品検査を実施しなければならないものは、重要安全部品(例:レーザー光源、レンズ等)やラベル・ラベリングである。
重要安全部品とは、当該部品の品質異常が製品全体の品質異常につながるものであり、しいて言えば患者やユーザの安全性に影響するものである。
つまり、当該供給品のリスクによっては、全品検査を実施しなければならないのである。
またラベルやラベリング(取扱説明書、添付文書等)は目視で構わないので、全品検査が求められる。
FDAは「ラベル・ラベリングの完全性」を要求している。万が一、ラベルやラベリングの内容に問題があったり、読めない場合などは安全性に直結するためである。
一方で、必ずしも全品検査は必要が無いけれども、抜き取り(サンプリング)で検査した方が良いものもある。
3Hとは
3Hとは「はじめて」「へんこう」「ひさしぶり」の頭文字をとったものである。
初めての取引業者の場合は、AQLの検査レベルを「きつい検査」にした方が良いかも知れない。
同様に変更直後の部品や、取引関係はあったものの長い間購入していなかった業者などの場合も、AQLの検査レベルを「きつい検査」にした方が良いかも知れない。
ダイナミックな検査レベルの変更
過去の歩留りデータをもとに、ダイナミックにAQLの検査レベルを「ゆるい検査」や「きつい検査」に変化させることも重要である。
供給業者のパフォーマンスが良ければ、自社の時間・労力・コストを使ってまで受領検査を実施する必要はない。
その場合は、AQLの検査レベルを「ゆるい検査」にすることも検討が必要である。
また、リスクの低い部品(ねじ等)や供給業者のパフォーマンスが極めて高い場合などは「検査なし」で良いかも知れない。 このように、購入した部品等の受領検査をリスクや供給者の能力に応じて適切なレベルで検査することが望まれる。